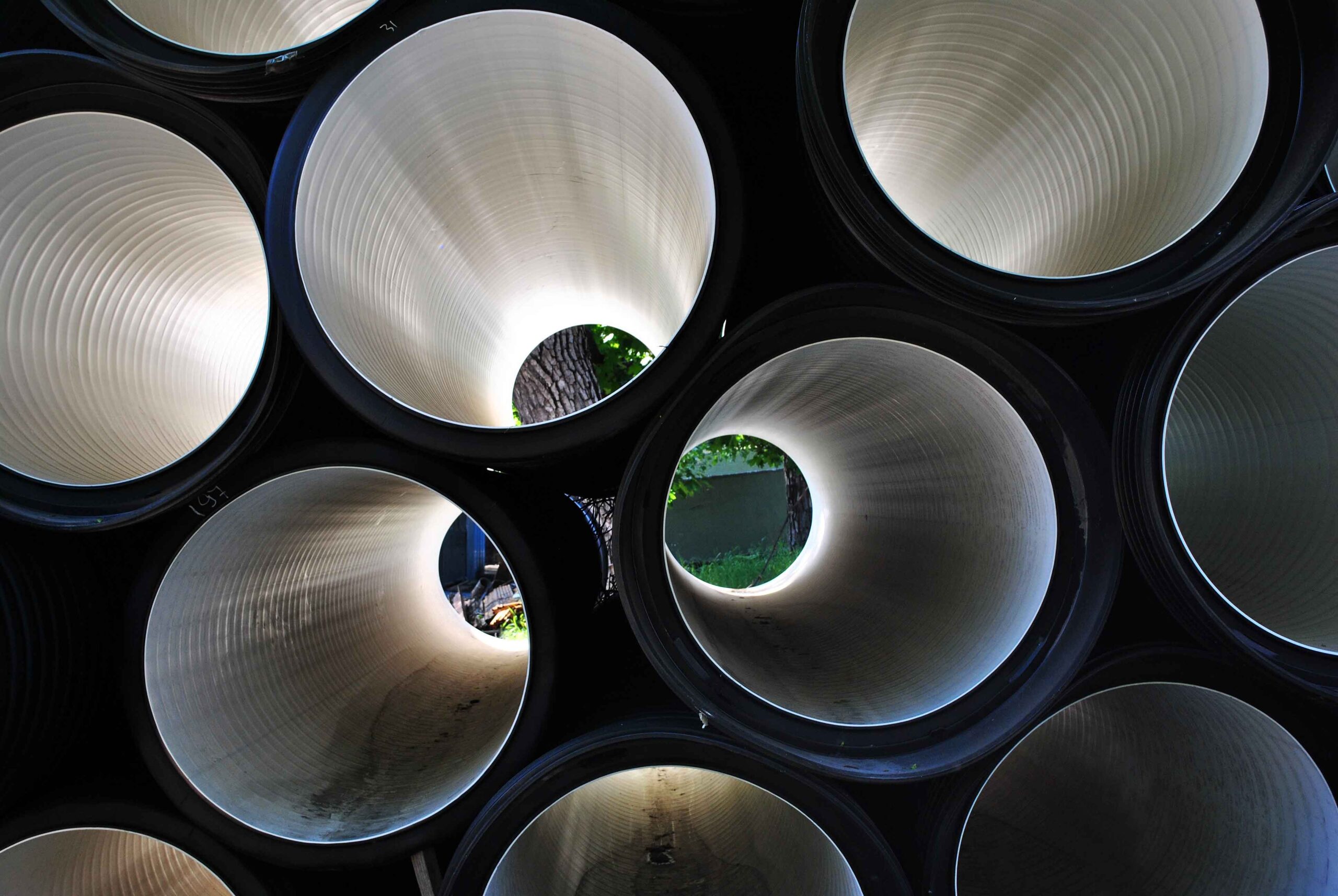
Rotary Impact Testing
Rotary Impact – from SGS Ludwig
Wear-resistant materials play a crucial role in various industries by minimizing damage caused by friction and wear. The solution is to use harder materials typically in the form for Chromium carbide or Tungsten carbide overlay, other hard coatings, cintered carbides or homogenous materials like white iron. Industry now has various commercial options for wear technologies, however within the mining industry there are other factors that come into play as rocks, boulders, frozen ore that can create impact damage.
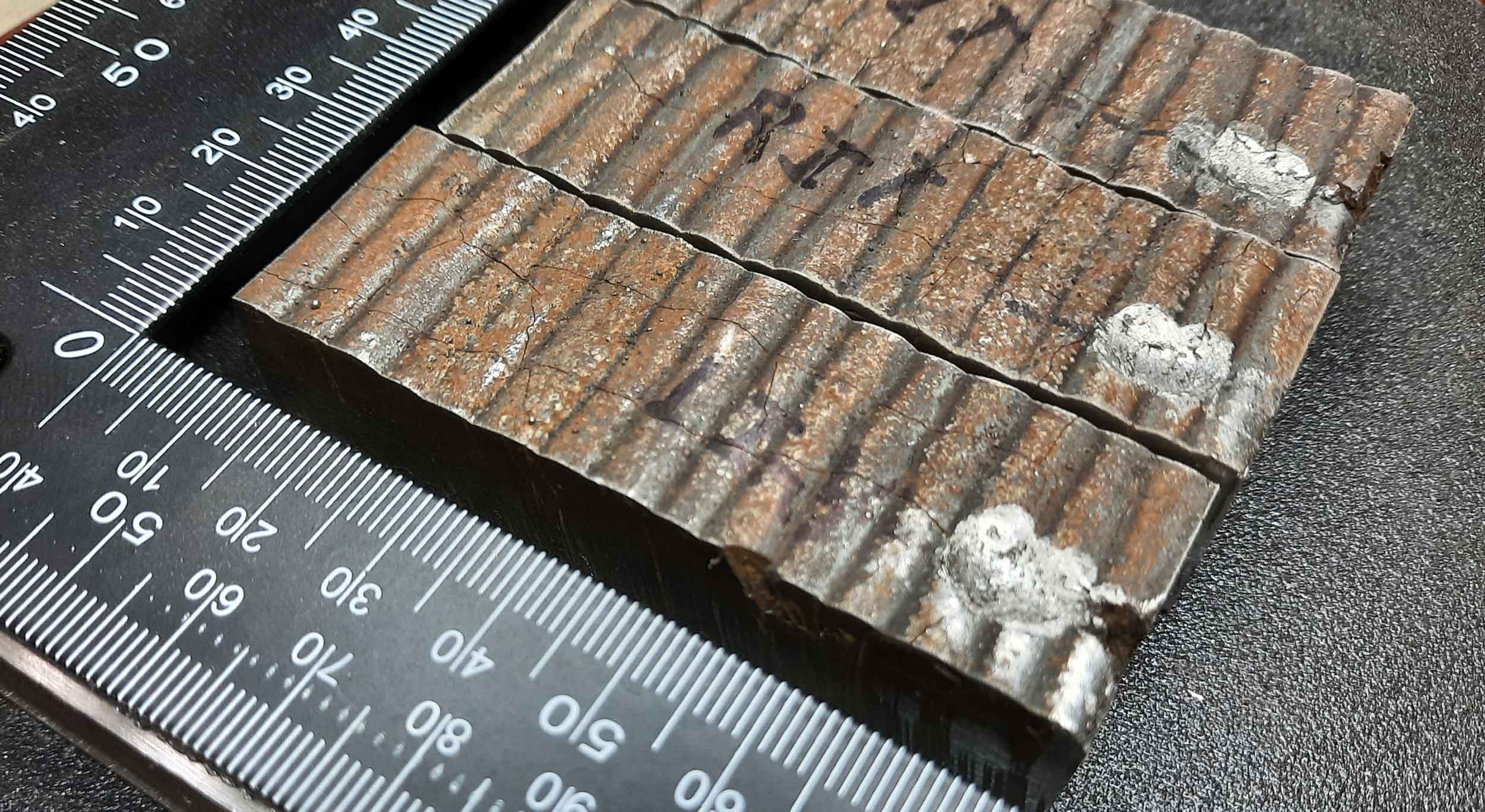
The Alberta Government testing subsidiary worked with mining industry producers and supplies who encounter significant impact and wear issues in their day to day operations. They developed a test to to determine a material’s ability to resist deformation when subjected to a sudden impulse load.
In 2020 SGS Ludwig purchased the design rights to build this testing apparatus. In 2023 the equipment went fully operational. Alberta producers now use this method for evaluating new materials as well as production testing to maintain conformity.
Rotary Impact Testing is requested within client specification in conjunction with ASTM G65 dry abrasion testing, metallurgical evaluation and image analysis. SGS Ludwig can help provide:
- ASTM G65 – methods A, B, C, D,E
- Optical Microscopy to 2000x
- Image Analysis software
- Scanning electron Microscope with EDX