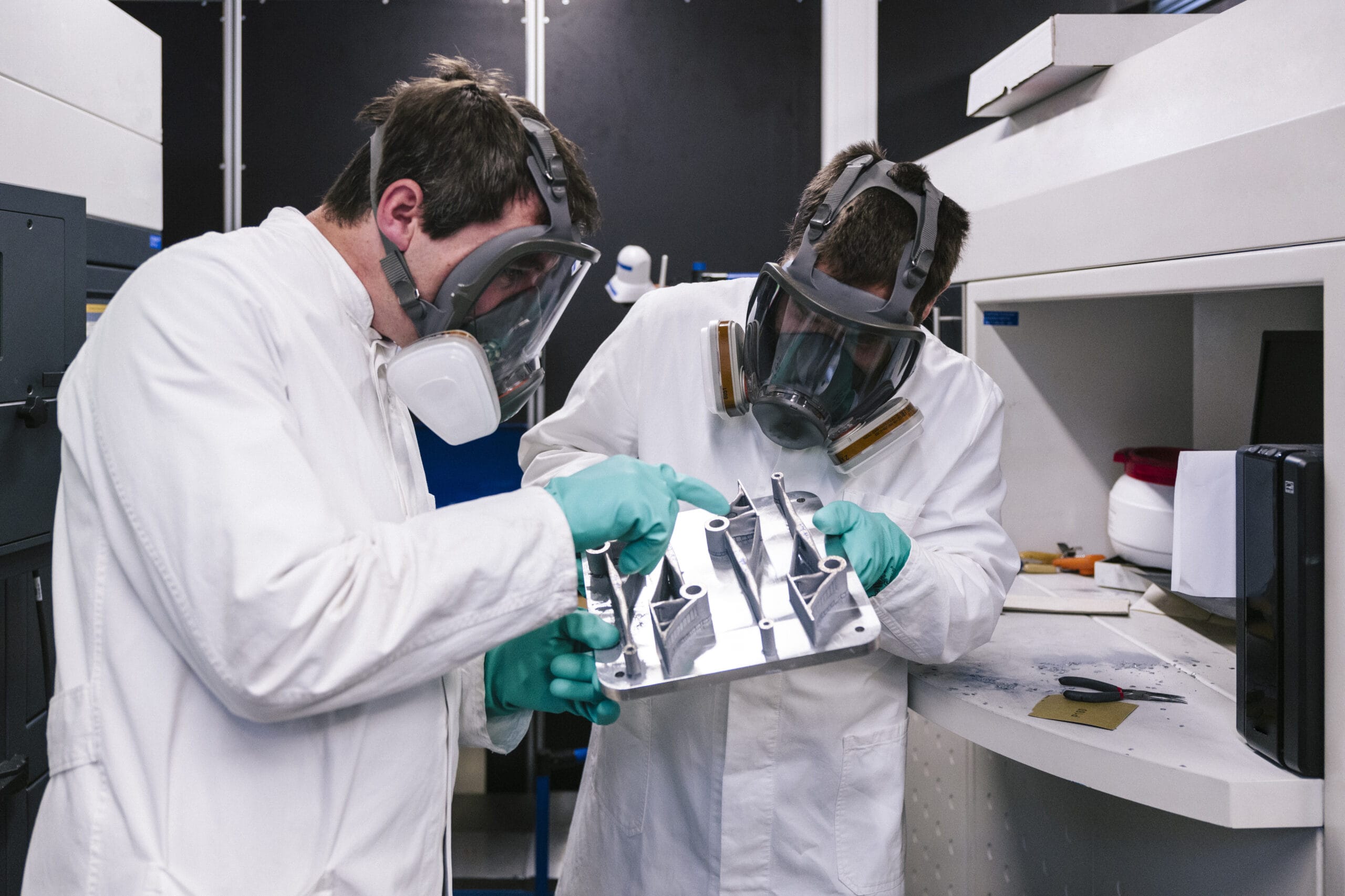
Why Us
Accreditations and Certifications
SGS MSi is part of the world’s leading testing, inspection and certification company, known as the global benchmark for quality and integrity.
ISO/IEC 17025
SGS MSi is ISO/IEC 17025 accredited by the American Association of Laboratory Accreditation (A2LA).
ISO/IEC 17025:2017 Certificate and Scope of Accreditation:

Nadcap
SGS MSi is accredited by the National Aerospace and Defense Contractors Accreditation Program. Nadcap (formerly NADCAP, the National Aerospace and Defense Contractors Accreditation Program) is a global cooperative accreditation program.
Nadcap Certificate
Scope of Accreditation – Materials Testing Laboratory
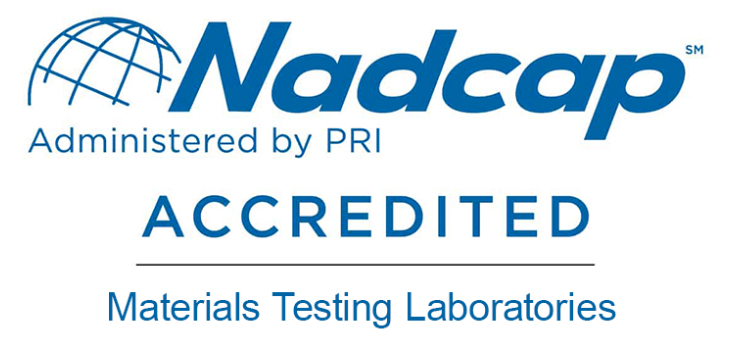
Our Commitment to Quality
As valuable contributors to SGS, the world’s leading inspection, verification, testing and certification company, it is the foremost responsibility of each employee to deliver services of the highest quality that fully satisfy the valid requirements of our customers. SGS Management is fully committed to:
- Continual improvement of all Quality systems.
- Establishing and regularly reviewing measurable Quality objectives at all levels and Functions.
- Reviewing this Quality policy for continuing suitability.
- As leaders in our profession, we want to project and live up to an image of integrity and professionalism.
To accomplish this, we shall:
- Promptly and courteously provide our external and internal customers with the information or service requested.
- Regard customer Satisfaction, Quality and Confidentiality as critical to business success.
- Create and preserve a work environment for all employees that fosters:
- Commitment to Quality
- Mutual trust and respect
- Teamwork
- Constant learning
- Breaking down of barriers
- Communication improvement
- Compliance with Safety, Health and Environmental Protection Regulations
- Recognition of individual and group achievements
- Develop and maintain our systems and work processes in accordance with internationally recognized Quality management standards.
- Measure the efficiency of our processes and our ability to meet external and internal customer’s valid requirements and expectations.
- Avoid conflicts of interest and accept only work which can be handled competently and professionally.
- Help employees identify and pursue opportunities to improve the Quality of their own work and to optimize the use of our resources.
- Correct shortcomings and act to correct situations that cause unsatisfactory performance.