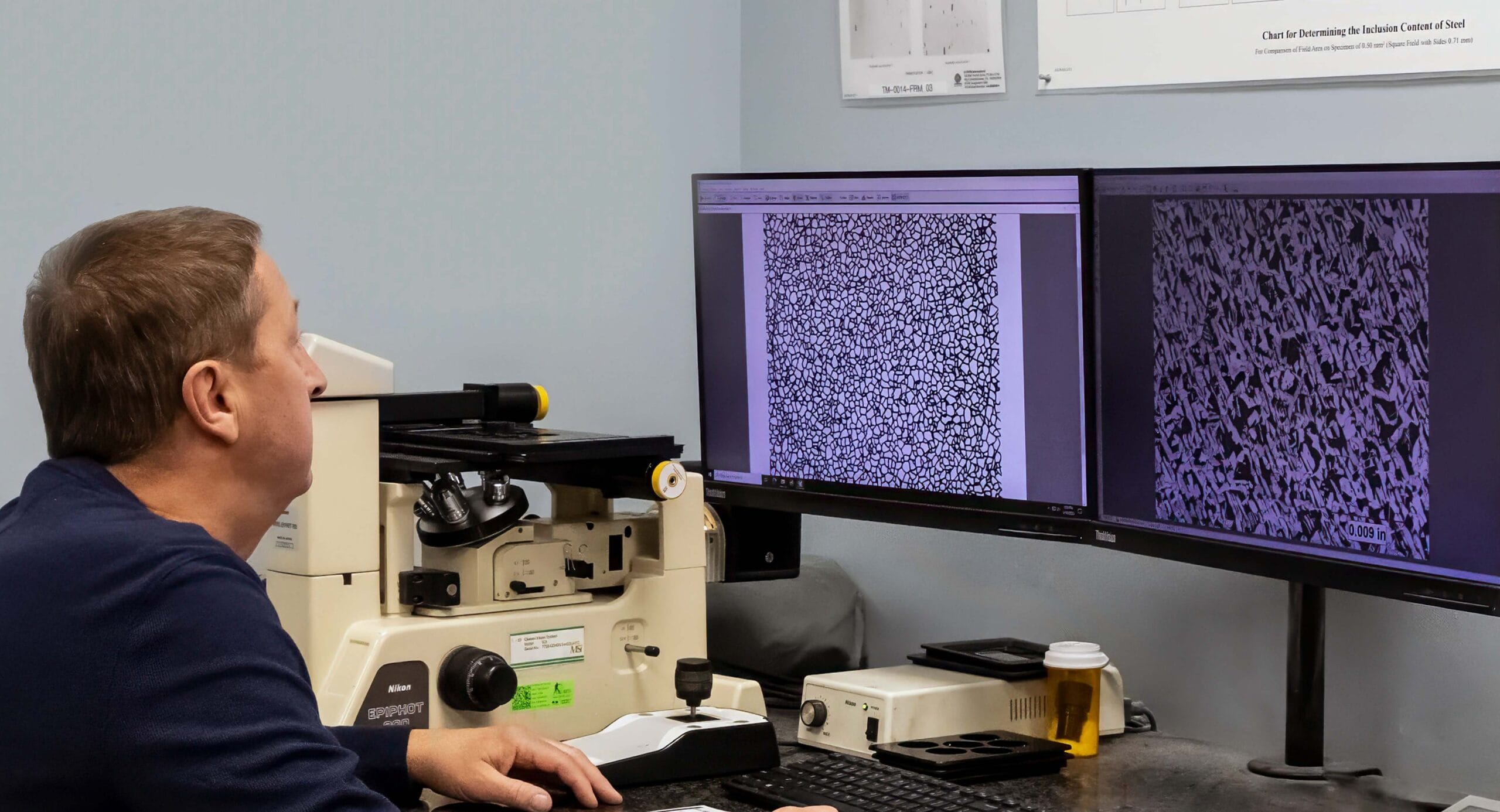
Metallurgical Services
Defect analysis of cast products manufactured from gray iron, ductile iron, cast steel, aluminum, stainless steel, or copper alloys, quite often include evaluation of surface or subsurface defects formed by entrapped gas.
Gas defects in castings are either endogenous (internal origin) or exogenous (external origin). Some of the causes of internal gas porosity are related to excessive gas content in the metal bath from charge materials, improper melting method and atmosphere, or inadequate deoxidation practice. Dissolved gases are then released during solidification. External gas defects can arise from molding or core materials that contain excessive moisture, improper amounts of core binders, or excessive amounts of additives containing hydrocarbons. Mechanical entrapment of external gas can also be related to the evacuation (venting) design of the mold package, improper mold permeability, or turbulence of hot metal in the sprue and runner system.
Gas Porosity Exam
Characterization and identification of the type and source of gas defects is performed by means of visual, stereoscopic, metallographic, and (energy dispersive spectroscopy) EDS methods. The size, shape, frequency, and identification of elements lining the cavities are documented and included in a detailed report to client. Suggestions to minimize or eliminate the gas defect are also provided.
Contact us today to learn more about our metallurgical testing services.
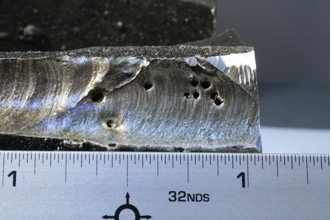