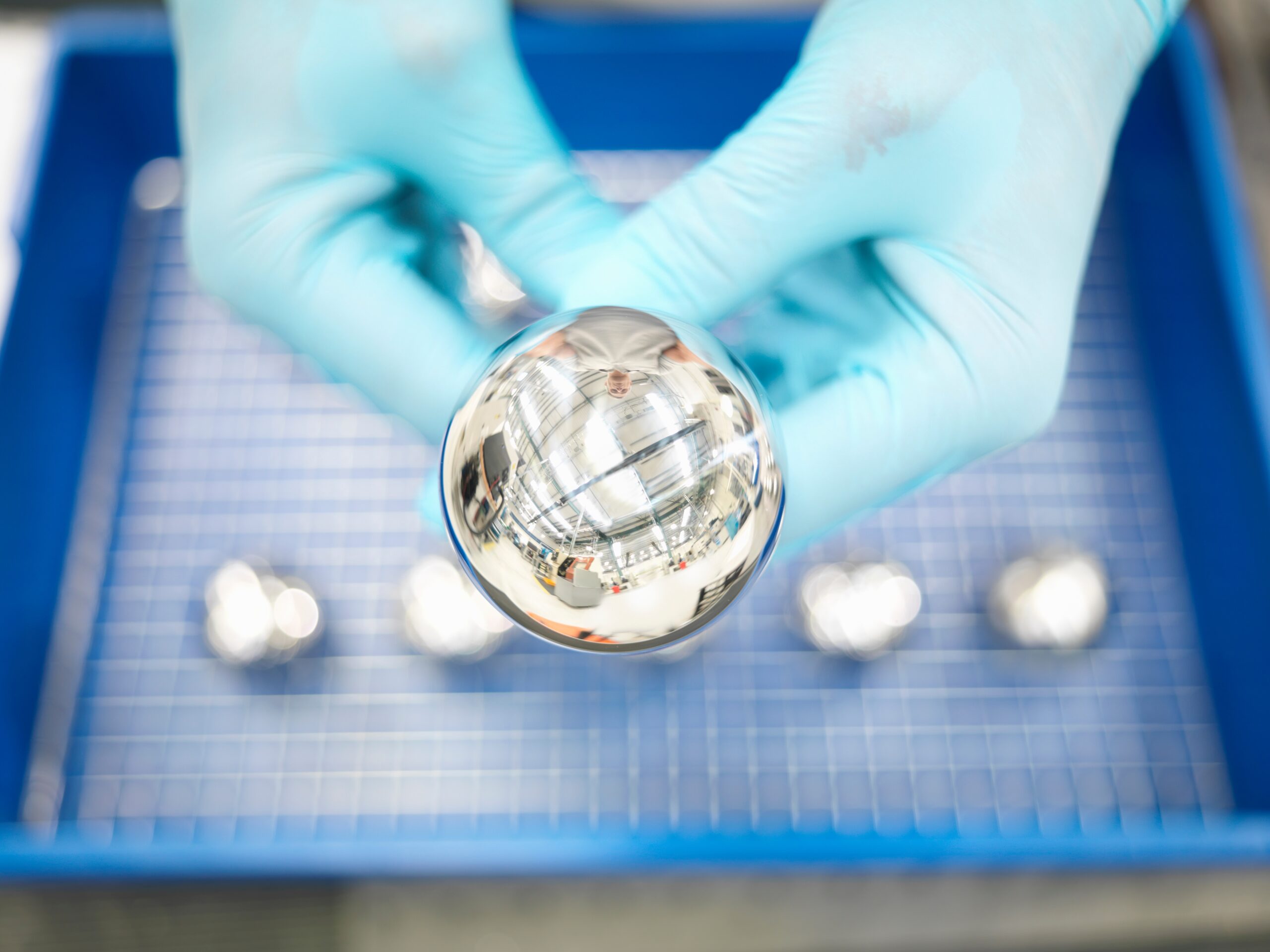
Industries Served
From precision tools that help diagnose patient conditions to implantables that improve their quality of life, medical devices play a vital role in everyday life
Understand the characteristics of the materials your medical devices are made of with reliable testing and engineering services from SGS MSi.
SGS MSi determines the chemical, mechanical, and metallurgical characteristics of materials using destructive examination methods. The clients we serve ultimately utilize the data obtained to ensure compliance. An A2LA and ISO/IEC 17025 accredited laboratory, our capabilities include:
- Specification Conformance
- Material Validation
- Supplier Qualification
- Raw Material Testing
- Root Cause Analysis
- EDM assessment
- Laser-Etch evaluation
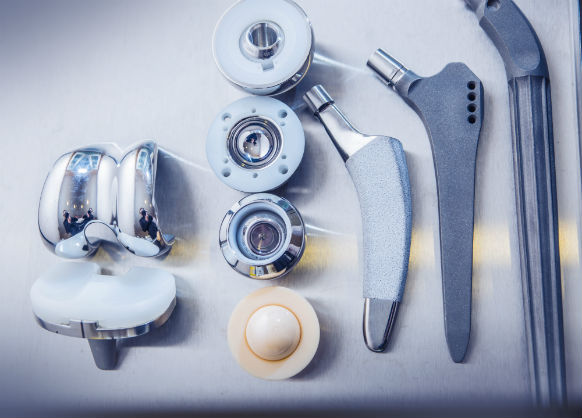
Chemical, mechanical, and metallurgical testing help product manufacturers and end users confirm the performance capabilities and establish operating ranges of materials manufactured into medical devices. With more than three decades of experience, our team of engineers, scientists, and technicians is well positioned to examine and validate your specimens. Common tests we perform for this industry include:
- Tensile
- Chemistry
- Bend
- Metallography
- Microstructure Analysis
- Inclusion Rating
- Grain Size
- Susceptibility to intergranular attack
We analyze a wide array of materials destined for use as medical devices. Some of them include:
- Titanium
- Cobalt-chromium
- Tantalum
- Stainless steel
- Nitinol
The equipment at our laboratory in Melrose Park, IL is calibrated regularly to certify accuracy. Calibration records are available upon request.
We provide a detailed report listing test type, parameters, and results obtained when analyzing materials. The language we use is clear and easy to understand. All engineering reportsare presented with a summary conclusion of our findings, any criterion supporting those results and, if appropriate, insights into possible failure avoidance.
Ensure materials are suitable for their intended use with reliable analyzing and certifying services from SGS MSi. With an unwavering commitment to quality, we’re your materials testing provider.
Contact us to learn more about our medical field materials testing and engineering services.
ASTM B338 | Standard Specification for Seamless and Welded Titanium and Titanium Alloy Tubes for Condensers and Heat Exchangers | ||
ASTM B348 | Standard Specification for Titanium and Titanium Alloy Bars and Billets | ||
ASTM F67 | Standard Specification for Unalloyed Titanium, for Surgical Implant Applications (UNS R50250, UNS R50400, UNS R50550, UNS R50700) | ||
ASTM F90 | Standard Specification for Wrought Cobalt-20Chromium-15Tungsten-10Nickel Alloy for Surgical Implant Applications (UNS R30605) | ||
ASTM F136 | Standard Specification for Wrought Titanium-6Aluminum-4Vanadium ELI (Extra Low Interstitial) Alloy for Surgical Implant Applications (UNS R56401) | ||
ASTM F138 | Standard Specification for Wrought 18Chromium-14Nickel-2.5Molybdenum Stainless Steel Bar and Wire for Surgical Implants (UNS S31673) | ||
ASTM F560 | Standard Specification for Unalloyed Tantalum for Surgical Implant Applications (UNS R05200, UNS R05400) | ||
ASTM F562 | Standard Specification for Wrought 35Cobalt-35Nickel-20Chromium-10Molybdenum Alloy for Surgical Implant Applications (UNS R30035) | ||
ASTM F1472 | Standard Specification for Wrought Titanium-6Aluminum-4Vanadium Alloy for Surgical Implant Applications (UNS R56400) | ||
ASTM F1537 | Standard Specification for Wrought Cobalt-28Chromium-6Molybdenum Alloys for Surgical Implants (UNS R31537, UNS R31538, and UNS R31539) | ||
ASTM F2063 | Standard Specification for Wrought Nickel-Titanium Shape Memory Alloys for Medical Devices and Surgical Implants | ||
ASTM F2229 | Standard Specification for Wrought, Nitrogen Strengthened 23Manganese-21Chromium-1Molybdenum Low-Nickel Stainless Steel Alloy Bar and Wire for Surgical Implants (UNS S29108) | ||
ISO 5832-2 | Implants for surgery — Metallic materials — Part 2: Unalloyed titanium | ||
ISO 5832-3 | Implants for surgery — Metallic materials — Part 3: Wrought titanium 6-aluminium 4-vanadium alloy |