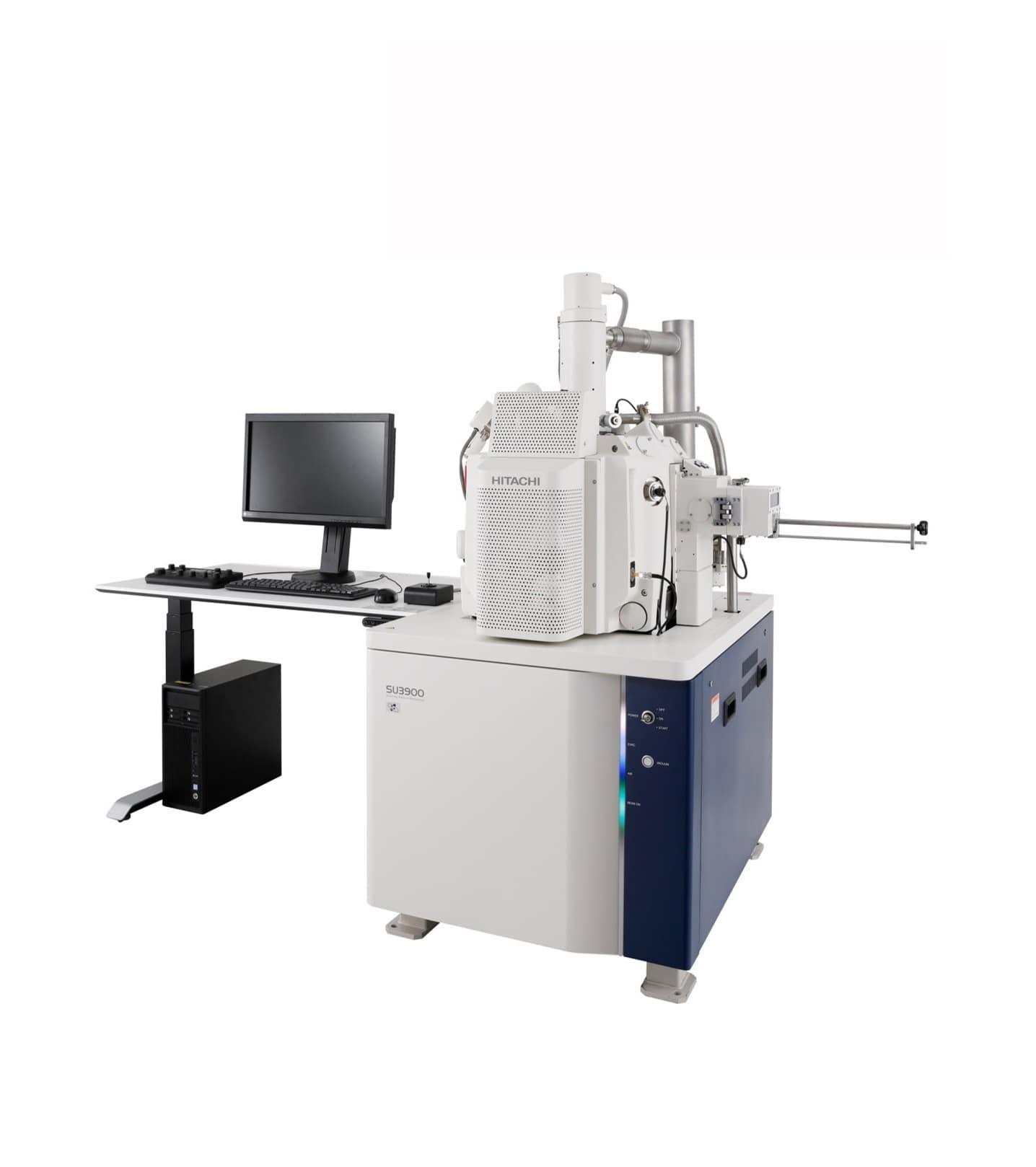
Metallurgical Services
Our Scanning Electron Microscopy department is the heart of all failure and corrosion analysis investigations
With over 30 years of experience our Scanning Electron Microscope (SEM) specialists are here to help you identifying the following failure mechanisms:
- Fatigue
- Intergranular Fractures
- Overload
- Hydrogen Embrittlement
- Wear
- Cavitation
- Ductile & Brittle Fractures
- Intergranular Corrosion
- Microbiological Corrosion
- Stress Corrosion
- Crevice Corrosion
- Galvanic Corrosion
- Pitting Corrosion
- Marine Corrosion
- Erosion
At SGS MSI we have state-of-the-art SEM, our Hitachi SU3900 is capable of high magnification images, secondary images in backscatter with the enhanced UVD detector, 3D modelling and image processing. The specimen chamber is one of the largest and can hold a 5” tall x 12” wide sample.
The in-chamber camera allows for an ease in analysis and navigation of one part or multiple samples during an evaluation.
The 3D modelling software allows measurements such as height between two points, volume, and simple surface roughness.
A SEM is an electron microscope capable of producing images of an object as small as 1nm. The electron beam interacts with the sample surface creating various signals of secondary electrons, backscatter electrons and x-rays. These signals are combined in a vacuumed chamber to produce an image of the material and form a high-resolution image that appears 3D to up to 10,000x magnification. Our variable pressure / environmental capabilities allow us to perform SEM analyses and evaluations on non-conductive specimen and parts.
SEM analysis is utilized for particle characterization, such as wear debris generated during mechanical wear testing. The high magnification, high-resolution imaging of our SEM analysis supports the determination of the number, size, and morphology of small particles, allowing clients to understand the wear properties of their material.
Fractography is a partial form of failure analysis that deals with crack growth and fracture characteristics of metals, components, and engineering structures. Fractography is categorized into fatigue, cleavage, and dimple rupture, to name a few fracture modes.
Our expertise in SEM used in conjunction with Energy Dispersive Spectroscopy (EDS) provides valuable information for our client’s material needs.
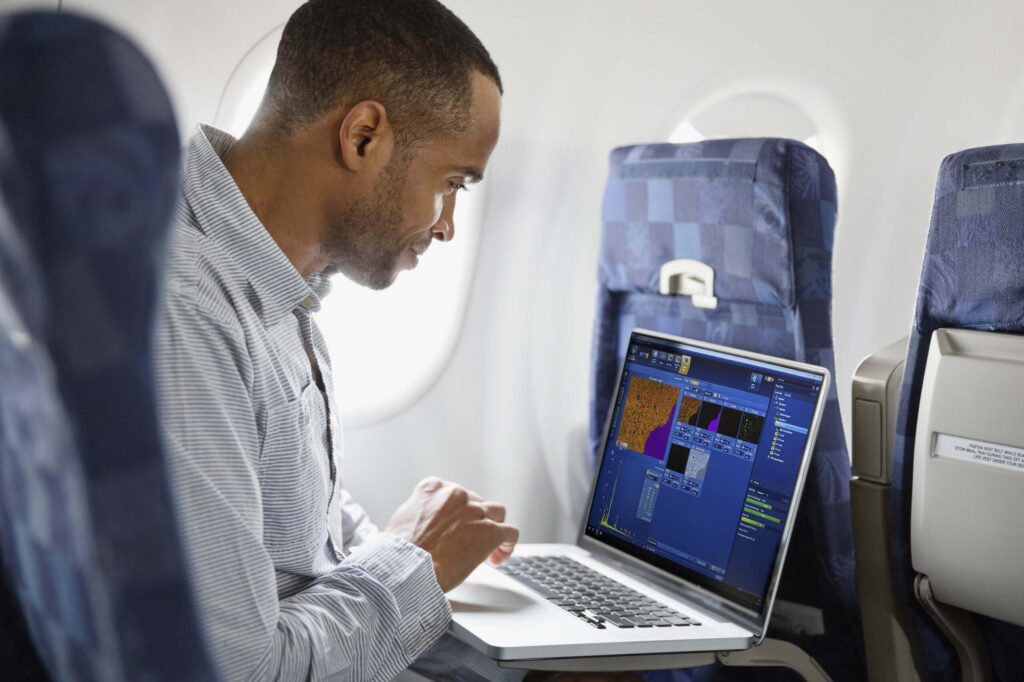
Anywhere SEM
Now you can access our SEM anytime you need! You can provide a sample to us and then you can watch the analysis as it happens! We will have a microscopist running the analysis while you direct them onto the keys points that you want analyzed. Once the data is collected, we can them share that information with you via cloud sharing or we can generate a report based on the data/finding of the analysis.
If there are multiple parties involved, they can direct the SEM/EDS analysis together with us and share the data around the world instantly. We can collaborate on your microanalysis projects and analyze your samples online without having to be on-site.
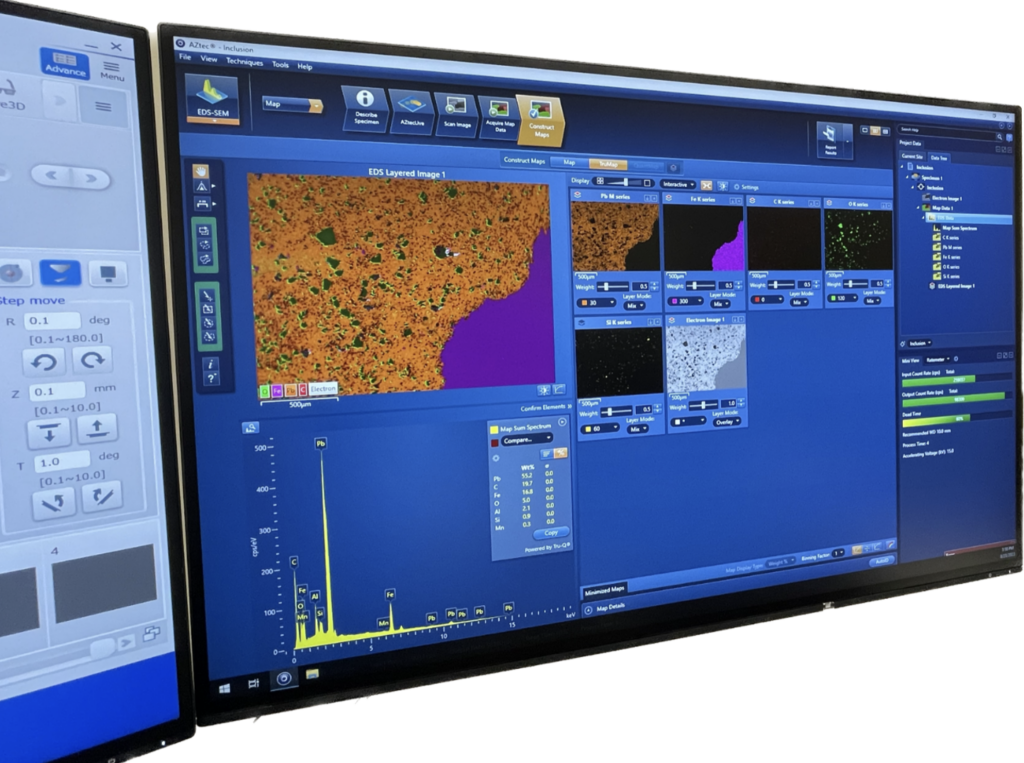
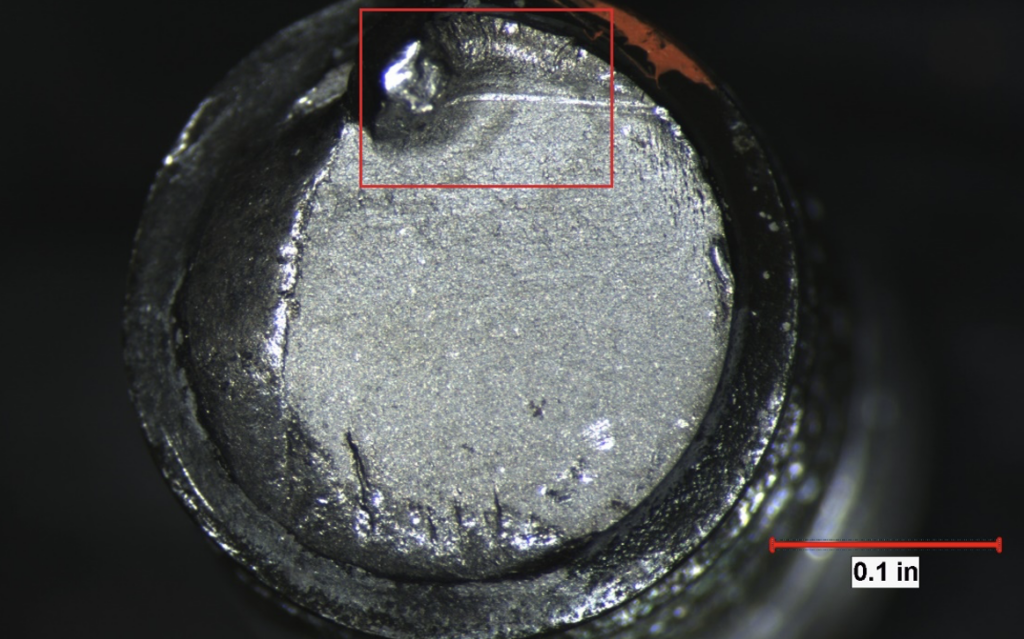
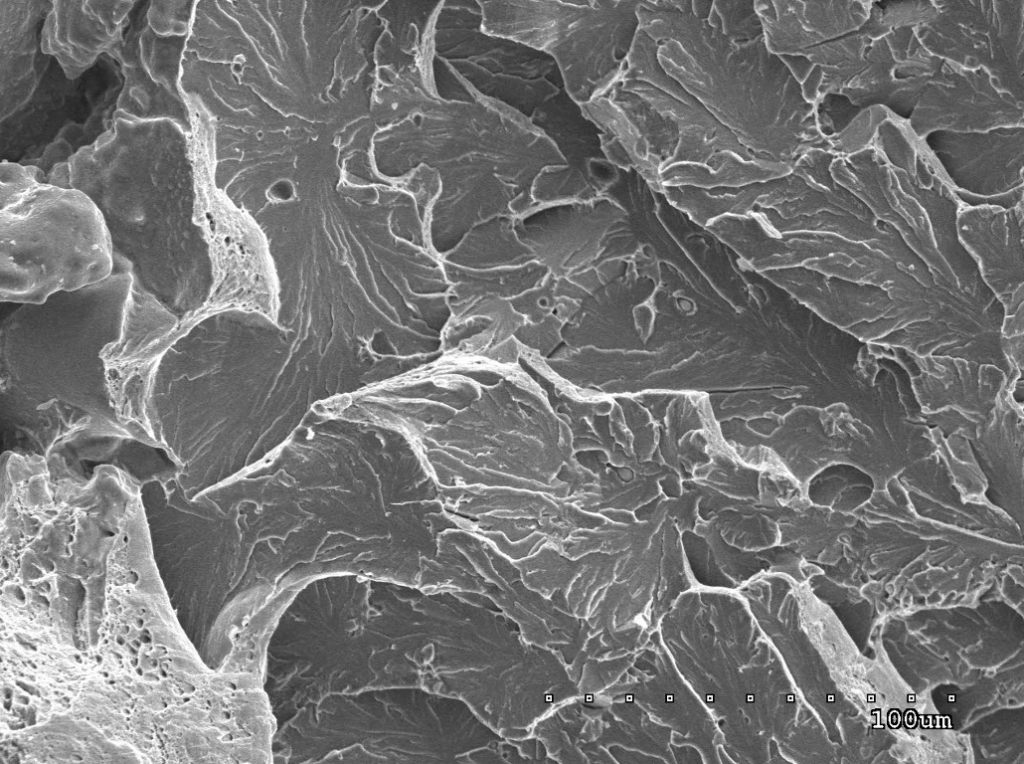
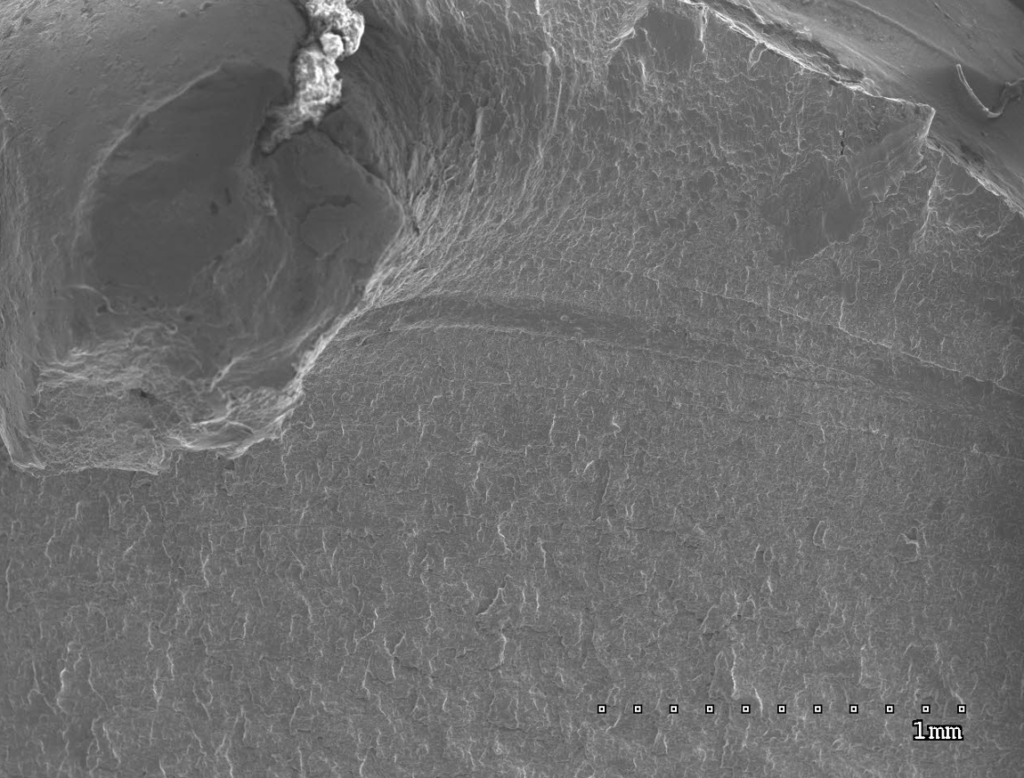
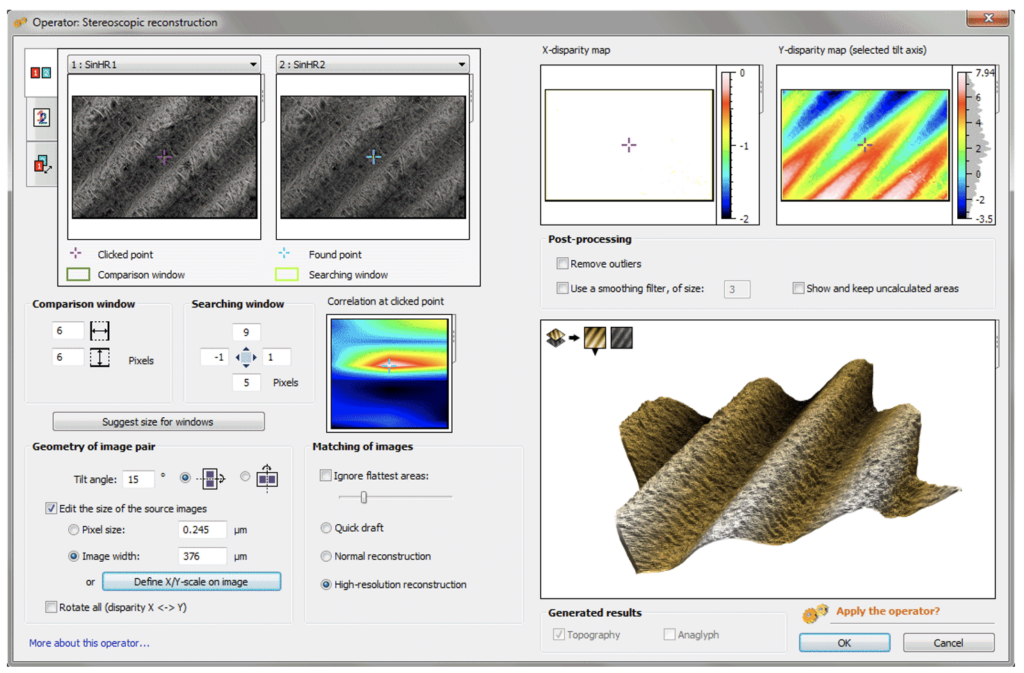
Test Methods and Specifications
The following is a listing of specifications that are in accordance with our A2LA and ISO accreditation.